Вступ
Висока вартість твердих сплавів і швидкорізальних сталей для різальних інструментів і їх невисока стійкість при експлуатації зумовило необхідність розробки методів для підвищення експлуатаційних властивостей ще на стадії виробництва.
Таким чином розроблено цілий ряд методів, які дозволяють підвищити зносостійкість і відповідно період стійкості різального інструменту від 1,5 до 8 раз. В основу цих методів закладено принцип, який полягає в тому, що зносостійкість інструменту гарантується за рахунок формування на поверхні тонких шарів інших матеріалів – покриттів. Серед таких методів найбільш перспективним є метод іонно-плазмового напилення. Даний метод є універсальним по можливості одержання широкої гами моношарових,багатошарових та композиційних покриттів на базі нітридних, карбідних, карбонітридних, оксидних, боридних та інших тугоплавких сполук металів ІV – VІ груп Періодичної системи елементів. З допомогою цього методу є можливість осаджувати якісні покриття при відносно низьких температурах нагрівання основного матеріалу. Крім того собівартість зміцненого інструменту є відносно невисокою і менша від вартості нового інструменту, а також забезпечує стабільне підвищення зносостійкості в 2,5-3,5 рази.
1 Загальна частина
1.1 Аналіз умов роботи різального інструменту
Процес різання – складний фізичний процес, що супроводжується значним тепловиділенням, деформаціями, спрацюванням різального інструменту і наростоутворенням на різці.
Впроцесі різання передня і задня частини леза різального інструменту підлягають значним перемінним навантаженням і знаходиться в стані рухомого контакту з оброблюваним матеріалом (рисунок 1.1). При цьому передня поверхня інструменту взаємодіє з прирізцевою поверхнею стружки, а задня поверхня – з поверхнею різання. Чим вища міцність і твердість оброблюваного матеріалу, тим більший тиск на контактних ділянках леза.
![]() |
Рисунок 1.1 [1]– Розподіл напружень на передній та задній поверхнях різального інструменту
Утворення стружки в процесі різання проходить під дією сили різання Р. Цю силу при токарній обробці розділяють на три складові (рисунок 1.2 ): тангенціальну Рz, що направлена вертикально вниз і визначає потужність різання, радіальну Py, що направлена вздовж поперечної подачі, яка віджимає різець і враховується при розрахунку міцності інструменту, осьову Px, що направлена вздовж повздовжньої подачі, яка віджимає різець в сторону супорта і враховується при визначенні допустимого навантаження на різець і механізми верстату при повздовжній подачі [1].
В процесі різання на сили Рz, Py, Px впливають оброблюваний матеріал, глибина різання, подача, передній кут різця, головний кут різця в плані, радіус заокруглення при вершині різця, МОР, швидкість різання та знос різця.
Для відрізних різців розрахункова сила різання Рz знаходиться в межах 300 – 500 Н [2].
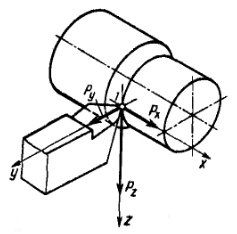
Рисунок 1.2 [1]– Складові сили різання
Максимальний тиск на контактних ділянках лез різних видів коливається в межах 10...60 ГПа [1]. Для порівняння: діючі навантаження на леза на два-три порядка перевищують навантаження на поверхні спряжень тертя деталей машин.
Під дією деформацій поверхневий шар оброблюваної поверхні зміцнюється. Ступінь зміцнення і глибина наклепу збільшується зі збільшенням подачі і глибини різання і зменшується зі збільшенням швидкості різання. Глибина наклепу приблизно в 2-3 рази більша при роботі із затупленим лезом. Мастильно-охолоджуючі рідини при різанні зменшують глибину і ступінь зміцнення поверхневого шару.
При деяких умовах різання на передню поверхню різальної кромки налипає оброблюваний метал, утворюючи наріст. По твердості він в 2-3 рази перевищує твердість оброблюваного матеріалу. При цьому він змінює геометричну форму різця, беручи участь в різанні негативно впливає на результати обробки, спрацювання різця і збільшуючи силу, що діє на різець. При обробці наріст періодично руйнується і знову утворюється. Ці явища погіршують якість обробки. Тому для зменшення наросту зменшують шорсткість передньої поверхні різального інструменту і по можливості збільшують передній кут і застосовують МОР.
При різанні металів затрачається робота на пластичні і пружні деформації в зрізаному шарі і в шарі, що прилягає до оброблюваної поверхні і поверхні різання, а також на подолання тертя по передній і задній поверхні різця. Робота, що затрачається на пластичні деформації, складає 80% роботи різання, робота тертя – 20%. Приблизно 85-90% всієї роботи різання перетворюється в теплову енергію, яка на 50-80% поглинається стружкою, на 10-40% – різцем, на 3-10% - оброблюваною деталлю [1]. Температура в зоні різання залежить від фізико-механічних властивостей оброблюваного матеріалу, режимів різання, геометричних параметрів інструменту і МОР. При обробці виділяється велика кількість тепла. Чим вища міцність і твердість оброблюваного матеріалу, тим вища температура в зоні контакту інструменту, яка при важких умовах роботи може сягати 1000 – 1100°С.
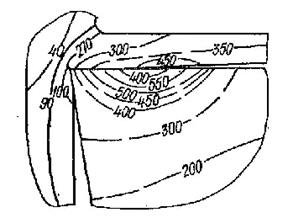
Рисунок 1.3 [3] – Температурне поле при типових режимах точіння різцем із швидкорізіальної сталі
Температура в зоні різання безпосередньо впливає на зносостійкість інструменту, стан оброблюваного матеріалу, якість поверхні та продуктивність різання.
Розглянемо будову механізму переміщення і різального інструменту – супорт токарно-гвинторізного верстата 16К20 (рисунок 1.4).
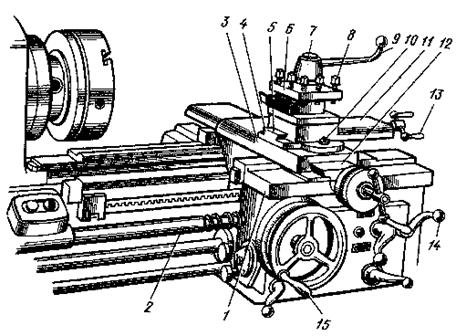
Рисунок 1.4 [2]– Супорт токарного верстата: 1 – нижні салазки; 2 – ходовий гвинт; 3 – поперечні салазки; 4 – поворотна плита; 5 – напрямні; 6 – різцетримач; 7 – гвинт; 8 – болти; 9 – рукоятка; 10 – гайка; 11 – верхні салазки; 12 – напрямні; 13, 14, 15 – рукоятки
Супорт призначений для переміщення під час обробки ріжучого інструменту, закріпленого в різцетримачі. Він складається з нижніх салазок (поздовжнього супорта) 1, які переміщаються по тих, що направляють станини за допомогою рукоятки 15 і забезпечують переміщення різця уздовж заготовки. На нижніх салазках по напрямним 12 переміщаються поперечні салазки (поперечний супорт) 3, які забезпечують переміщення різця перпендикулярно осі обертання заготовки (деталі). На поперечних салазках 3 розташована поворотна плита 4, яка закріплюється гайкою 10. По напрямних 5 поворотної плити 4 переміщаються (за допомогою рукоятки 13) верхні салазки 11, які разом з плитою 4 можуть повертатися в горизонтальній площині щодо поперечних салазок і забезпечувати переміщення різця під кутом до осі обертання заготовки (деталі). Різцетримач (різцева головка) 6 з болтами 8 кріпиться до верхніх салазок за допомогою рукоятки 9, яка переміщається по гвинту 7. Привід переміщення супорта проводиться від ходового гвинта 2, від ходового валу, розташованого під ходовим гвинтом, або уручну. Включення автоматичних подач проводиться рукояткою 14.
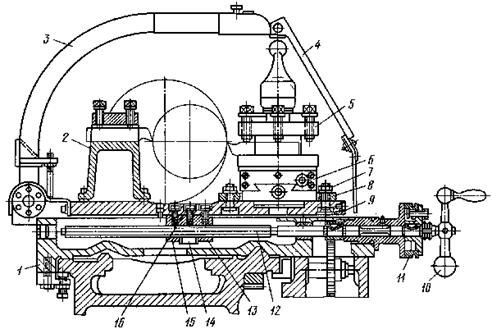
Рисунок 1.5 [2] – Поперечний супорт токарно-гвинторізного верстата: 1 – поздовжній супорт; 2 – задній різцетримач; 3 – кронштейн; 4 – щиток; 5 – різцетримач; 6 – верхні салазки; 7 – гайки; 8 – поворотна плита; 9 – поперечні салазки; 10 – рукоятка; 11 – лімб; 12 – ходовий гвинт; 13, 15 – гайки; 14 – клин; 16 – гвинт
Пристрій поперечного супорта показаний на рисунку 1.5. По напрямним повздовжнього супорта 1 ходовим гвинтом 12, оснащеним рукояткою 10, переміщаються салазки поперечного супорта. Ходовий гвинт 12 закріплений одним кінцем в подовжньому супорті 1, а іншим - пов'язаний з гайкою (що складається з двох частин 15 і 13 і клину 14), яка кріпиться до поперечних салазок 9. Затягуючи гвинт 16, розсовують (клином 14) гайки 15 і 13, завдяки чому. вибирається зазор між ходовим гвинтом 12 і гайкою 15. Величину переміщення поперечного супорта визначають по лімбу 11. До поперечного супорта кріпиться (гайками 7) поворотна плита 8, разом з якою повертаються верхні салазки 6 і різцетримач 5. На деяких верстатах на поперечних салазках 9 встановлюється задній різцетримач 2 для проточки канавок, відрізки і інших робіт, які можуть бути виконані переміщенням поперечного супорта, а також кронштейн 3 з щитком 4, що захищає робочого від попадання стружки і МОР.
Пристрій різцетримача показаний на рисунку 1.6 [лист КП.ТВ – 11.00.000 СК]. У центруючій розточці верхніх салазок 5 встановлена конічна оправка 3 з різьбовим кінцем. На конусі оправки встановлена чотиристороння різцева головка 6. При обертанні рукоятки 4 головка 2 переміщається вниз по різьбі конічної оправки 3 і через шайбу 1 і упорний підшипник забезпечує жорстку посадку різцевої головки 6 на конічній поверхні оправки 3.
Рисунок 1.6 – Різцетримач: 1 – шайба; 2 – головка; 3 – конічна оправка; 4 – рукоятка; 5 – верхні салазки; 6 – різцева головка; 7 – штифти
Від повороту при закріпленні різцева головка утримується кулькою, яка заклинюється між поверхнями, утвореними пазом на основі конічної оправки 3 і отвором в різцевій головці 6. При необхідності змінити позицію інструменту рукоятку 4 повертають проти годинникової стрілки. При цьому головка 2 повертається і переміщається вгору по різьбі конічної оправки знімаючи зусилля затягування різцевої головки 6 на конусі конічної оправки 3. Одночасно головка 2 повертає різцеву головку 6 за допомогою гальмівних колодок, фрикційних пов'язаних з поверхнею розточки головки 2 і з’єднаних з різцевою головкою 6 штифтами 7. При цьому кулька, розташована у основи конічної оправки 3, не перешкоджає повороту різцевої головки, оскільки він втоплюється в отвір, стискаючи пружину. Якщо в процесі роботи рукоятка 4 (у затиснутому положенні) почала зупинятися в незручному положенні, то, змінюючи товщину шайби 1, можна встановити її в зручне для робочого положення.
Технічні характеристики токарно-гвинторізного верстата моделі 16К20:
- діаметр обробки, мм:
над станиною, 400;
над поперечним супортом – 200;
- найбільший діаметр оброблюваної деталі, мм – 50;
- відстань між центрами, мм – 710, 1000, 1400, 2000;
- частота обертання шпинделя, об/хв – 12,5 – 1600;
- подача, мм/об:
повздовжня – 0,05 – 2,8;
поперечна – 0,025 – 1,4;
- потужність електродвигуна, кВт – 10.
1.2 Аналіз основних видів спрацювання різального інструменту
В процесі різання в результаті взаємодії оброблюваного матеріалу з інструментальним контактні ділянки на передній і задній поверхнях спрацьовуються. Спрацювання контактних ділянок проходить безперервно, протягом вього процесу різання, практично при будь-яких умовах різання і фізико-механічних властивостях як інструментального так і оброблюваного матеріалів [4].
При будь-якому виді обробки матеріалів різанням частина матеріалу, яка збирається з заготовки (стружка), ковзає по передній поверхні різального елементу інструменту і одночасно частина задньої поверхні різального клину ковзає по обробленій поверхні. Тертя, що виникає на цих обох поверхнях, є тертям ковзання. При різанні трибологічні процеси можуть мати адгезійну, дифузійну і абразивну природу, відбувається частіше вього внаслідок реалізації одночасно декількох механізмів взаємодії.
В залежності від умов різання і властивостей інструментального і оброблюваного матеріалу знос спостерігається по задній поверхні, по передній поверхні або по задній і передній поверхнях одночасно (рисунок 1.7). Також спостерігається знос, пов’язаний із заокругленням ріжучої кромки.
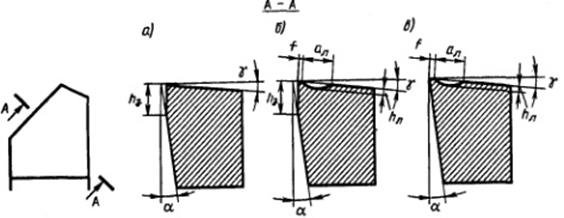
Рисунок1.7 [1] – Спрацювання леза різального інструменту:
а – по задній поверхні; б – одночасно по задній і передній поверхнях; в – по передній поверхні; f – ширина фаски; ан – довжина лунки; hл – глибина лунки; hз – ширина ділянки зносу по задній поверхні
Знос по задній поверхні спостерігається частіше при малій товщині зрізу, особливо при обробці крихких матеріалів (чавун, кремній і т.д.) [4]. Знос по передній поверхні має місце, коли задня поверхня захищена від зношування наростом, або коли температура передньої поверхні значно перевищує температуру задньої поверхні. Особливістю зносу передньої поверхні є утворення лунки на деякій відстані від ріжучої кромки. По мірі спрацювання глибина лунки hл зростає, а радіус кривизни зменшується. Зазвичай довжина лунки росте в сторону ріжучої кромки повільніше, ніж в протилежну сторону. При одночасному зносі по передній і задній поверхнях ділянка поверхні f, що знаходиться між лункою і ріжучою кромкою, поволі зменшується з обох сторін, зменшується кут загострення і в результаті міцність ріжучої кромки знижується, що призводить до руйнування різальної частини інструменту.
Норми спрацювання токарних різців:
- для швидкорізальних сталей hз= 1,5...2 мм, hл = 0,35...0,45 мм;
- для твердих сплавів hз= 0,8...1 мм, hл = 0,8...2 мм [1].
Знос різального інструменту прийнято класифікувати по таким видам: адгезійно-втомний, абразивний, дифузійний, хіміко-абразивний і окислювальний [1].
Адгезійно-втомний знос. При ковзанні одної поверхні по іншій проходить безперервний процес зрізання і виникнення адгезійних зв’язків. Безперервне схоплювання і зрізання в окремих точках контакту найбільш інтенсивно проходять при різанні металів. Поверхня інструменту знаходиться під дією зрізуючих напружень. В результаті цього процесу частинки металу місцями вириваються з поверхні. Зазвичай таке виривання значно більше зі сторони мякого металу при ковзанні по більш твердому, проте має місце процес переносу частинок більш твердого металу на більш мякий (адгезійний знос). Адгезійно-втомне спрацювання різального інструмента може спостерігатись в результаті крихкого руйнування контактних шарів, і характеристикою зносостійкості матеріалу буде границя міцності σw. В інших умовах Адгезійно-втомне зношування може спостерігатись в результаті пластичного зрізу контактних шарів інструментального матеріалу і його характеристикою буде границя текучості σт і твердість HV[4].
Зрізання з’єднань контактних поверхонь в адгезійних ділянках може відбуватися різними способами. Якщо міцність з’єднання в адгезійних ділянках менша міцності самих матеріалів, то зріз проходить по поверхні з’єднання. При цьому знос є незначним. Якщо з’єднання міцніше, ніж один з металів, то зрізання проходить в глибині менш міцного металу. Коли міцність з’єднання вища міцності обох матеріалів, то зрізання, як правило проходить в глибині менш міцного, але в окремих випадках є ймовірність зрізання і більш міцного матеріалу на його втомлених ділянках. Якщо в процесі деформації поверхонь матеріал в контактних шарах зміцнюється то відбувається глибинне виривання. При цьому пошкодження поверхонь досить значні. Міцність матеріалу різального інструменту в контактних шарах зони тертя повинна бути вищою, ніж оброблюваного матеріалу і тому зрізання адгезійних плям чи ділянок, як правило буде відбуватись по оброблюваному матеріалу і в окремих ділянках – по втомлених ділянках матеріалу інструменту.
Абразивний і хіміко-абразивний знос. Механізм абразивного спрацювання полягає в тому, що тверді включення оброблюваного матеріалу, впроваджуючись в контактні поверхні інструменту, дряпають ці поверхні, діючи як мікроскопічні різці. Найбільш сильно абразивний знос проявляється в тому випадку, коли твердість різальної частини інструменту в процесі різання падає, оброблюваний матеріал зміцнюється. На рисунку представлені мікрофотографії задньої поверхні різців із сталі Р6М5 при різанні сталі 40Х в середовищі повітря і чотирихлористого вуглецю. При різанні на повітрі на передній поверхні утворюється наріст, який періодично руйнується. Часто твердість частинок наросту, що руйнується є вищою, ніж інструментального матеріалу, тому вони в процесі різання спричиняють абразивне спрацювання контактних поверхнонь інструменту. Аналогічну дію викликають карбіди, оксиди та інші абразивні включення. Абразивний механізм є ведучим видом спрацювання різального інструменту.
Хіміко-абразивне спрацювання відбувається під дією абразиву в хімічно активних середовищах. При роботі інструменту з швидкорізальної сталі хімічно-активні середовища підсилюють спрацювання поверхонь, в результаті чого зменшується стійкість інструменту. При обробці твердими сплавами, навпаки, хімічно активні середовища підвищують стійкість інструменту, так як адгезійно-втомний знос знижується, а абразивно-хімічний проявляється слабо.
Дифузійний знос. При різанні з високими швидкостями починає проявлятись дифузійний механізм руйнування леза різального інструменту, який є наслідком:
- дифузії основних компонентів матеріалу в оброблюваний матеріал. Ці компоненти розчиняються в оброблюваному матеріалі (стружці) і видаляється з ріжучих поверхонь;
- дифузії вторинних компонентів матеріалу інструменту з тонкого поверхневого шару, що призводить до зміни його механічних властивостей;
- дифузії компонентів оброблюваного матеріалу в матеріал інструменту, що веде до зміни фізико-механічних характеристик поверхневого шару інструменту.
Висока температура, інтенсивна адгезія, великі пластичні деформації і тиски в зоні контакту при високих швидкостях різання повинні в значній степені сприяти взаємному дифузійному розчиненню компонентів інструментального і оброблюваного матеріалів. Частина інструментального матеріалу переходить в матеріал деталі і стружку. Тому сумарний знос різального інструменту буде включати в себе спрацювання, викликане розчиненням матеріалу різального інструменту в оброблюваному матеріалі, тобто знос, викликаний дифузією. По мірі збільшення швидкості різання дифузійний перенос стає домінуючим фактором, що визначає механізм спрацювання інструменту.
Окислюючий знос. В проміжку між контактуючими поверхнями інструментального і оброблюваного матеріалів виникає газове або рідинне середовище. Якщо це є повітря, то кисень з повітря безперервно окислює тонкий поверхневий шар інструментального матеріалу. Оксидний шар, який утворюються на поверхні є крихкий і в процесі різання руйнується. Тому для підвищення зносостійкості необхідно виключити попадання повітря на котактні поверхні застосуванням захисних газів (азот, аргон).
1.3 Аналіз методів зміцнення різального інструменту
На даний момент всі методи зміцнення різального інструменту поділяють на такі види:
- нанесення зносостійких покриттів;
- нанесення антифрикційних покриттів;
- механічні методи зміцнення;
- хіміко-термічні методи зміцнення (азотування, цементація, карбонітрування);
- гальванічні методи зміцнення (омідення, нікелювання);
- фізичні методи зміцнення (лазерне зміцнення, обробка холодом).
Механічне зміцнення. При механічному зміцненні підвищення механічних властивостей досягається механічною чи фізичною дією на дефектний шар з метою усунення негативних наслідків попередньої обробки. Задача вирішується двома способами: а) видаленням дефектних шарів з робочої поверхні інструмента; б) наступною термічною обробкою інструмента або механічною дією на дефектний шар з метою покращення мікроструктури і підвищення механічних властивостей.
При правильно вибраних режимах шліфування і наступної доводки чи полірування робочих поверхонь інструмента підвищується міцність і однорідність механічних властивостей. В результаті застосування абразивної обробки з використанням синтетичних алмазів і надтвердих матеріалів на основі нітрида бору стійкість різального інструмента підвищується приблизно на 30%.
Електролітичне полірування.У випадку коли складно застосовувати фінішну доводку використовують електролітичне полірування. При цьому нерівності поверхні зтравлюються і поверхня вирівнюється. При цьому зникають головним чином лише риски і шорсткості. Тому якість поверхні після електролітичного полірування гірша, ніж після механічної доводки. Даний процес проводять у ваннах. Катодами слугують пластини (свинець, графіт), анодом – інструмент. Електроліт вибирається в залежності від оброблюваного матеріалу. Сталі зазвичай полірують в суміші сірчаної і ортофосфорної кислот з добавкою хромового ангідриду. Для забезпечення якісного полірування необхідно чітко додержувати режим процесу. В деяких випадках для підтримання високих густин струму необхідні потужні джерела постійного струму.
Застосовують електролітичне полірування для стружкових канавок свердл, мітчиків, розверток, кінцевих фрез. Операція виконується перед фінішним шліфуванням і заточуванням. Електролітичне полірування рекомендується застосовувати для інструменту, що підлягає хромуванню.
Ультразвукова і термоультразвукова обробка. Методи ультразвукової і термоультразвукової обробки дозволяють значно покращити властивості інструментальних сплавів. Застосовуючи ультразвукові коливання в процесі термообробки швидкорізальних сталей вдалося підвищити стійкість інструменту в 1,5-2 рази. Ультразвуковій обробці піддають інструменти із швидкорізальних сталей після гартування, і також готовий інструмент.
В основі ультразвукової обробки лежать принципи безпосередньої дії ультразвукових коливань великої потужності на кристалічну структуру сплавів. Ефективність ультразвукової обробки на структуру і властивості металів залежить від потужності ультразвуку, тривалості обробки і місця в технологічному процесі.
Застосування ультразвукової обробки загартованої сталі перед відпусканням може бути рекомендовано для інструменту, від якого потрібні найбільш високі значення механічних властивостей. Обробка загартованої сталі здійснюється безпосередньо після гартування при 20ºС в масляній ванні. Тривалість обробки 30 – 60 хвилин. Під дією ультразвукових коливань в швидкорізальних сталях проходить природнє термічне старіння.
Найменш трудомістким процесом при зміцненні інструменту є термоультразвуковий відпуск. Одночасна дія температури і ультразвукових коливань на загартовану швидкорізальну сталь викликають структурні перетворення, що й при звичайному відпуску. Ультразвукові коливання позитивно впливають на властивості сталей, в тому числі на твердість, границі міцності на згин, зносостійкість і ударну в’язкість. При необхідності отримання найбільш високих значень теплостійкості сталі застосовують подвійний термоультразвуковий відпуск. Процес проводять при температурах 600 - 620ºС. Тривалість відпуску – 20 хвилин.
Нанесення зносостійких і антифрикційних покриттів.
Іонно-плазмове напилення. Нанесення зносостійких покрить методом конденсації з йонним бомбардуванням. Отримання покрить цим методом полягає у випаровуванні тугоплавких матеріалів електричною вакуумною дугою в середовищі реагуючих газів і наступної конденсації з йонним бомбардуванням парів матеріалів з реагуючими газами, які утворюються внаслідок плазмо-хімічних реакцій. Перевага цього методу – низький температурний режим (400-600°С), що дозволяє наносити покриття як на твердосплавний інструмент, так і на інструмент із швидкорізальної сталі. Стійкість напилених інструментів зростає в 2-8 раз [5].
Метод іонного розпилення полягає в бомбардуванні розпилюваного матеріалу прискореним потоком позитивно заряджених іонів. Частіше за все для цієї мети використовують тліючий розряд при невисокому вакуумі в камері – від 1 до 1·10-1 Па.
На матеріал, що розпилюється подають від’ємний потенціал і він виконує в тліючому розряді роль катода. Для утворення позитивно заряджених іонів в розряді використовують аргон та інші гази, які подаються в камеру через спеціальний пристрій. Якщо в камеру подати активні гази (CO2, N2), то відбувається реакційне напилення покриття.
На практиці отримали розповсюдження діодна, тріодна та магнетронна схеми іонного розпилення.
Діодна схема. Розпилюваний матеріал у вигляді диска або пластини товщиною декілька міліметрів та розміром поверхні близької до площі поверхні виробу, що напилюється, закріплюється на водоохолоджуваному катоді, до якого підводять від’ємний потенціал (рисунок 1.8). Другий електрод – анод, який розміщується на відстані декілька сантиметрів від катода. В деяких випадках анод може бути опорою для закріплення виробу. На анод подається позитивний потенціал. Разом з камерою він знаходиться під потенціалом землі.
Рисунок 1.8 – Схема діодної системи іонного розпилення [6]:
1 – високовольтний ввід; 2 – вакуумна камера; 3 – екран; 4 – катод; 5 – пластина (мішень); 6 – темний катодний простір; 7 – позитивний стовп дуги; 8 – підложка; 9 – анод; 10 – патрубок до вакуумної системи; 11 – частинки, що осаджуються; 12 – іони; 13 – подача газу
Для полегшення ініціювання тліючого розряду використовують допоміжний анод. Умови існування тліючого розряду при діодній схемі ускладнені. Тому процес здійснюється при максимально високому тиску робочого газу, який допускається в межах від 1 до 10 Па та напрузі від 5 до 10 кВ. Густина іонної сили струму не перевищує 5 мА/см2.
Швидкість розпилення катода і конденсації досить мала (від 0,2 до 2 нм/с). При діодній схемі утворюються вторинні високоенергетичні електрони (3-5 кВ), які бомбардують поверхню напилення, сприяючи нагріванню виробу.
Діодну схему використовують в основному для напилення тонких плівок при виробництві інтегральних схем. Для напилення захисних покриттів ця схема малоефективна.
Тріодна схема. Вона є більш ефективною ніж діодна, значною мірою усуває її недоліки. Процес здійснюється при більш низькому тиску робочого газу (10-1 і нижче). При цьому продуктивність процесу збільшується в декілька разів.
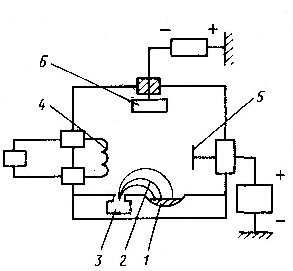
Рисунок 1.9 – Схема установки іонного осадження з тріодною системою та додатковою іонізацією газоподібного матеріалу електронним променем [7]:
1 – мішень; 2 – промінь; 3 – високовольтна електронно-променева гармата; 4 – термокатод; 5 – анод; 6 – виріб
Тріодна схема має наступні особливості (рисунок 1.9). Гарячий катод в даній схемі є додатковим джерелом електронів. Для збудження розряду, між гарячим катодом і анодом подають високу напругу – 1-2 кВ. Найбільша ефективність іонізації газу досягається за рахунок надання електронам складного руху, завдяки магнітній котушці. Магнітне поле, діючи на тліючий розряд, змінює характер руху електронів. На більш „важкі” іони магнітне поле діє слабше. Електрони здійснюють рух навколо магнітних ліній по спіралі. Збільшується ефективна довжина шляху електронів і тому збільшується ступінь іонізації газу. Допоміжний катод, анод і котушка утворюють генератор плазми, незалежно від розпилюваного матеріалу і виробу. Напруга, що подається на катод не впливає на розряд, який утворює плазму. Це дозволяє регулювати напругу, не доводячи її до високих рівнів.
На розпилюваний матеріал (холодний катод) подається від’ємна напруга – 0,7-1 кВ. Створюються умови пришвидшення іонів з області гарячого катода у напрямку розпилюваного матеріалу. На анод подається позитивне зміщення відносно виробу. Це запобігає переміщенню електронів до виробу і знижує можливість його перегрівання.
Магнетронна схема. Порівняно з іншими схемами дозволяє досягти вищих показників густини іонного струму і швидкості розпилення.
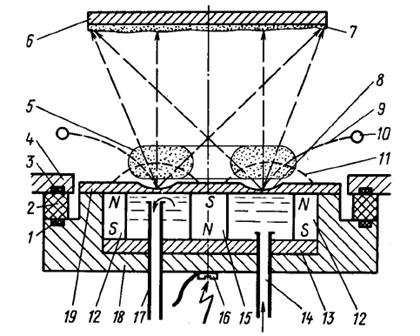
Рисунок 1.10 – Схема кільцевого планарного магнетрона [6]:
1,3 – ущільнення; 2 – ізолююче кільце; 4 – фланець; 5,8 – зони плазми і ерозії; 6 – підложка; 7 – осаджене покриття; 9,11 – електричне і магнітне поля; 10 – анод; 12,15 – периферійні і центральні магніти; 13 – основа магнітного блоку; 14,17 – трубки для циркуляції води; 16 – зажим; 18 – корпус; 19 – мішень
Під розпилюваним матеріалом (катодом) встановлюють постійні магніти (рисунок 1.10). Силові лінії у вигляді дуги замикаються між полюсами N-S, утворюючи неоднорідне магнітне поле. Над катодом розміщують кільцевий анод. Коли подають постійну напругу 300-1000 В, між катодом і анодом утворюється електричне поле напруженістю Е і виникає тліючий розряд. Силові лінії електричного поля перпендикулярні поверхні катода та магнітним силовим лініям. Завдяки схрещеному магнітному та електричному полям електрони від катода переміщуються по циклоїді. В площині паралельній площині електрода створюється область замкненого дрейфу. Відбувається багатократне зіткнення електронів з молекулами робочого газу, завдяки чому підвищується ступінь його іонізації і зростає концентрація бомбардуючих іонів поблизу матеріалу, який розпилюється.
В кільцеподібній зоні ступінь іонізації робочого газу наближається до 100%. Це дозволяє досягти густини іонного струму 10-20 мА/см2. завдяки цьому швидкість розпилення наближається до більш продуктивних систем вакуумно-конденсаційного напилення. Межа швидкості розпилення визначається теплопровідністю розпилюваного матеріалу, умовами його охолодження. Водяне охолодження матеріалу запобігає його високому нагріванню і плавленню. Процес здійснюється при тисках від 10-1 до 10-2 Па. Магнетронні системи дозволяють напиляти покриття виробів із складною конфігурацією, наприклад зовнішні та внутрішні поверхні циліндричних виробів.
Вимоги, необхідні для підвищення надійності та довговічності роботи елементів машин і конструкція обумовили розробку серії технологічних процесів, що забезпечують одержання зносостійких покриттів на основі нітридів і карбідів перехідних металів. Широке промислове застосування одержав метод конденсації із іонізованого потоку речовини, розроблений в Харківському фізико-технічному інституті, що отримав назву КІБ. Було впроваджено такі установки для зміцнення, як „Булат”, ВУ–1Б, „Пуск”, ИЭТ-84 та інші, в основі яких закладено використання електродугових випаровувачів катодної форми для створення потоків осаджуваної речовини. Установка „Булат-3”, яка має ручне управління вакуумною системою, універсальна як по типах оброблюваних деталей, так і по видах нанесених покриттів (багатошарові, композиційні), добре пристосована для проведення дослідних робіт. Недоліком вищезгаданих установок є невисока продуктивність.
В даний час використовують модернізовані установки для напилення зносостійких покриттів: „Булат-4”, „Булат-6”, серія ННВ та інші. Зміцнення різального інструменту в установці ННВ6.6-И1 здійснюється у вакуумній камері 1 (рисунок 1.11). Для фокусування плазмового потоку передбачена плазмооптична система 4. Матеріал, що розпилюється виконаний у вигляді циліндричного катоду 4. Анодом є стінки вакуумної камери. Створення вакууму в камері здійснюється з допомогою вакуумних насосів 6. Для отримання нітридних покриттів в камеру подається азот. Випаровувач 4 і підложка з інструментами 2 мають окремі джерела живлення 7 і 8.
В установці ННВ6.6-И1 реалізовано ефективну технологію для нанесення титано-нітридних покриттів на різноманітний різальний інструмент, яка поєднує в собі простоту діодної схеми іонного розпилення і ефективність магнетронної схеми завдяки магнітному фокусуванню плазмового потоку. Установка має механізм, що забезпечує планетарне переміщення оброблюваних деталей в камері. Це дає можливість зміцнювати будь-який ріжучий інструмент довжиною до 400 мм, довжиною робочої частини до 250 мм, діаметром до 400 мм. За один цикл (2-4 години) в установці можуть бути зміцнені 2500 свердл діаметром 5 мм або 16 черв’ячних фрез довжиною 100 мм і діаметром 100 мм [8].
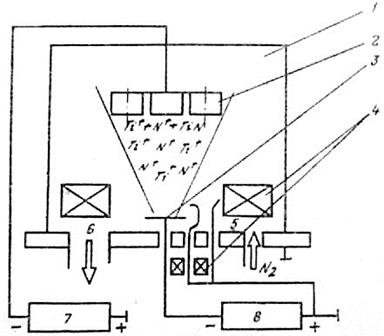
Рисунок 1.11 [10] – Схема установки для іонно-плазмового напилення: 1 – вакуумна камера; 2 – різальний інструмент; 3 – випаровувач (катод); 4 – плазмооптична система; 5 – напуск реакційного газу; 6 – вакуумна система; 7,8 – джерела живлення
Весь технологічний цикл зміцнення відрізних різців з нанесенням покриття TiN полягає в наступних операціях:
- підготовка інструменту (час на завантаження 15-20 хвилин);
- забезпечення вакууму в камері (30- 45 хвилин );
- іонне бомбардування і осадження TiN покриття (35-40 хвилин);
- охолодження інструменту (25- 45 хвилин);
- підйом камери, видалення металічної пилюки, відвантаження інструментів, установка наступної партії інструментів (7-10 хвилин).
На основі дослідів і практичному застосуванні різців покритих нітридом титану TiN методом КІБ визначено, що стійкість при обробці конструкційних вуглецевих сталей підвищена в 5-5,9 раз, а при обробці високолегованих сталей в 2-3 рази.
Електролітичне хромування. Спосіб покращення поверхневого шару хромуванням використовують в основному для пуансонів, штампів, форм лиття під тиском, робочих елементів вимірювальних інструментів, прес-форм.
Електролітичне хромування виконується при температурах 50 – 75ºС. Тому його можна використовувати для сталей будь-якої теплостійкості. Інструменти хромують після викінчувальної обробки – термообробки, шліфування і заточування. Після хромування для зменшення залишкових напружень необхідно провести відпуск при температурі 150ºС протягом одної години.
Покриття хромом відзначаються високою зносотійкістю і твердістю, що сягає HV 900-1100. Висока твердість зберігається до температури 400°С. Хромові покриття мають низький коефіцієнт тертя, що сприяє підвищенню зносостійкості поверхонь. Недоліком хромових покрить є зниження втомної міцності сталі на 20-30% після хромування. Тому для різальних інструментів цей вид обробки застосовують рідко.
Хімічне нікелювання. Ці покриття можуть наноситись на робочі поверхні різального інструменту як хімічним, так і електрохімічним шляхом. Головною перевагою хімічно осадженого покриття являється його рівномірне нанесення на ділянках складного профілю, тому хімічний метод найбільш вигідний для складнопрофільного фасонного або вимірювального інструменту.Стійкість різального інструменту збільшується в 1,5-4 рази.
Хімічне нікелювання проходить без накладання струму за рахунок відновлення іонів металу із розчинів його солей гіпофосфітом натрію. Нікелеві покриття, відновлені гіпофосфітом, містять 10-15% фосфору.
Покриття мають добре зчеплення з основним металом, високу твердість і зносостійкість, що можуть бути підвищені після термічної обробки. Твердість покриття не знижується навіть при гранично-допустимих температурах для інструменту із швидкорізальної сталі. Проте поряд з цим хімічно осаджене покриття відзначається крихкістю при товщині більше 10 мкм, і викришується при згині чи ударі. Тому оптимальна товщина покриття вибирається в межах 5-9 мкм. Позитивним фактором даного покриття є пористість, яка добре втримує МОР на робочих поверхнях.
Для нанесення покриття рекомендований наступний технологічний процес:
- обезжирення в органічному розчиннику. В якості розчинників використовують бензин, уайт-спіріт, трихлоретилен;
- хімічне чи електролітичне обезжирення в розчині їдкого натрію, кальцинованої соди, тринатрійфосфату з добавкою емульгатора;
- травлення з метою видалення окисних плівок, наданню поверхні необхідного мікрорельєфу і забезпечення хорошого зчеплення покриття з основою. Проводять в суміші сірчаної і соляної кислот шляхом занурення на 15 – 20 с і промивання в холодній воді;
- хімічне нікелювання. В склад розчину входять: 30 г/л хлористого нікелю, 20 г/л оцетнокислого натрію, 1 г/л йодистого калію. При температурі 90 – 95°С величина осадженого покриття за 30 хвилин складає 6 мкм;
- промивання в холодній воді;
- промивання в гарячій воді;
- термічна обробка.
Мікротвердість покриття без термообробки Н = 5000...5500 МПа. З допомогою термообробки можна підвищити твердість і силу зчеплення з основою. Для дрібнорозмірного інструменту (діаметром до 5 мм) рекомендується: нагрівання при температурі 200 – 250° С, витримка 2 години, охолодження на повітрі. При цьому досягається твердість 8000...9000 МПа без помітного зниження ударної в’язкості.
Детонаційне напилення. В інструментальному виробництві детонаційні покриття наносять на калібри та вимірювальний інструмент, фільєри для протяжки дроту, пуансони, інструменти для глибокої витяжки, спіральні і трубчасті свердла, фрези, мітчики, різці, полотна ножів.
Суть операції нанесення покриття полягає в наступному. Довга труба, закрита з одного кінця заповнюється вибуховою сумішшю, в яку вприскують порошок напилюючого матеріалу (рисунок 1.12). Запалювання суміші здійснюється з допомогою іскри. Продукти вибуху разом з частинками матеріалу покриття рухаються в трубі з великою швидкістю. Вийшовши з труби, потік частинок попадає на поверхню заготовки і утворює покриття.
В якості вибухової суміші використовують киснево-ацетиленову суміш. Обладнання для детонаційного нанесення покриттів є стаціонарним. Оскільки рівень шумів при вибухах сягає 120 – 150 дБ, установки розміщують в звукоізоляційних боксах, а процес керується з пульта. Частота вибухів 4 – 5 за секунду. Для переміщення інструментів використовують маніпулятори і транспортери.
При нанесенні покриття інструмент не підлягає помітному нагріванню. Інструменти з твердосплавним покриттям можна заточувати і доводити алмазними кругами. Товщина покриття 75-100 мкм.
1 – твердосплавна суміш; 2 – труба; 3 – ланцюг запалювання; 4 –
змішувач; 5 – вентилі; 6 – балон.
Фізико-хімічні методи зміцнення інструменту.
Ціанування. Насичення поверхневого шару вуглецем, азотом чи ціанування є завершальною операцією. Ціанування проходить при температурах не нижче 480°С і інтенсивно розвивається з підвищенням температури до 580°С. Швидкорізальні сталі ціанують при температурі 550-570°С, не викликаючи зниження твердості прилеглих шарів. Товщина шару, отримана при цій температурі, залежить від тривалості процесу і становить 0,02-0,07 мм. Твердість інструментів, що підлягають ціануванню, повинна бути не нижче HRC 62 для того, щоб тонкий ціанований шар розміщувався на твердій основі.
Ціанований шар представляє собою тонку суміш мартенситу, карбідів і карбонітридних фаз і має підвищену теплостійкість та зносостійкість, зменшує коефіцієнт тертя і налипання металу. Стійкість інструментів підвищується в 1,5-2 рази.
В залежності від середовища розрізняють рідинне, газове і тверде ціанування. Найбільш оперативним процесом є рідинне ціанування, тривалість якого складає 5 – 30 хвилин.
Для рідинного ціанування швидкорізальних сталей як правило застосовують такі розчини у ваннах: а) 50% NaCN, 25-30% Na2CO3, 10-15% NaCl; б) 50% NaCN, 15 -20 % Na2CO3, 15 -20 % NaCl. Для стабільності процесу необхідно підтримувати постійний тепловий режим ванни, відкриваючи її тільки при завантаженні і вивантаженні. Інструмент завантажується невеликими партіями і нагрітими до 400°С. Роботи необхідно проводити в ізольованому приміщенні з припливно-витяжною вентиляцією і пунктом нейтралізації.
Газове ціанування проводиться в суміші аміаку і вуглекислого газу. Температура процесу 550 – 570 °С, витримка – 1-2 години. Виконують ціанування в спеціальних герметичних камерах.
Тверде ціанування не потребує спеціального обладнання, так як його можна проводити в печі для відпуску. Його виконують в суміші 60 -70% деревного вугілля і 30-40 % жовтої кров’яної солі.
Сульфоціанування. Сульфоціанування – це процес насичення поверхні металу одночасно вуглецем, азотом і сіркою. На поверхні сталі виникає плівка сульфіду заліза товщиною 3-6 мкм, що виконує роль твердого мастила. Сульфоціанування підвищує зносостійкість дещо більшу ніж ціанування у випадках недостатнього змащування, а також на інструментах, що мають велику площу контакту з оброблюваною деталлю (мітчики, розвертки, фасонні різці).
Рідке азотування. Суть методу полягає в тому, що інструмент після звичайної термічної обробки і заточування підлягає нагріванню в розплаві азотовмісних солей з метою насичення його поверхні азотом і вуглецем. Ванна для рідкого азотування має такий склад: 28-40% NaCNO, 28-40% KCl, 25-45% кальційованої соди.
Процес азотування складається з таких операцій: 1) підігріванні інструменту до 400-450°С; 2) рідкого азотування при температурі 550°С; 3) охолодження і промивання в гарячій та холодній воді. Рідкому азотуванню підлягає інструментах як новий, так і відновлений, виготовлений із всіх марок швидкорізальної сталі після кінцевої термічної і механічної обробки. Твердість зміцненого шару і його вплив на стійкість такий самий, як при ціануванні. Перевагою рідкого азотування є той фактор, що процес оснований на застосуванні нетоксичних солей, що полегшує включення цієї операції в технологічний процес.
Іонне азотування. Метод іонного азотування здійснюється в плазмі тліючого розряду. Суть процесу полягає в наступному. З допомогою електричного поля азот у формі іонів бомбардує поверхню виробу і насичує її (рисунок 1.13). У вакуумній печі 1 знаходяться інструменти 2, ізольовані від стінок посудини. Інструменти зв’язані з негативним полюсом 3 і представляють собою катод газового розряду. Заземлена стінка вакуумної печі – анод. У вакуум між стінкою печі та інструментами подається азотовмісний газ під тиском 1Атм. Після вмикання високої напруги запалюється розряд в газі. Відбувається процес іонізації газу, в результаті чого іони азоту бомбардують поверхю інструменту і насичують поверхню.
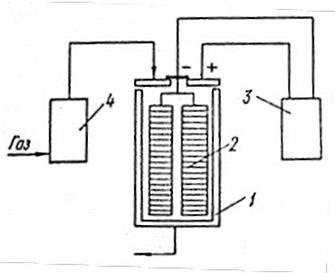
Рисунок 1.13 [5]– Схема установки для іонного азотування
1 – камера; 2 – виріб; 3 – джерело живлення; 4 – пристрій
газозабезпечення.
Особливо ефективним є застосування іонного азотування для фрез, що заточуються по передній поверхні. В цьому випадку нітрований шар зберігається при переточках по задній поверхні. Стійкість азотованих зуборізних фрез підвищується в 4-8 разів, черв’ячних фрез – в 2-3 рази.
1.4 Технічне і економічне обгрунтування зміцнення різця відрізного
В зв’язку з невеликим терміном експлуатації різального інструменту із швидкорізальної сталі (40 – 60 хвилин) розроблено ряд ефективних методів для підвищення його стійкості. Метод нанесення зносостійких покриттів, завдяки відносно простим технологіям нанесення, універсальності, високій ефективності покриття отримав найбільше розповсюдження серед сучасних методів зміцнення і активно впроваджується у інструментальне виробництво.
Серед перерахованих у пункті 1.3 методів нанесення зносостійких покриттів вигідно вирізняється метод іонно-плазмового напилення. Цей метод дозволяє отримати зносостійкі покриття (карбіди і нітриди металів), які підвищують стійкість інструменту в середньому в 3,0 рази (таблиця 1.1).
Таблиця 1.1 – Досвід застосування різальних інструментів з покриттями нанесених методом КІБ
Тип і матеріал інструменту |
Оброблюва ний матеріал |
Тип покриття |
Режим різання |
Коефіцієнт підвищення стійкості |
Фреза дискова Р18 |
38 ХМЮА |
TiN |
V=30 м/хв S=50 мм/хв |
3 |
Розвертка Р18 |
12Х18Н10Т |
TiN |
V=2,3 м/хв S=0,2 мм/об |
2 |
Фреза кінцева Р6М5 |
12Х18Н10Т |
TiN |
V=11 м/хв S=60 мм/хв |
2,5 |
Фреза кінцева Р18 |
Сталь 45 |
Mo2N |
V=67,5 м/хв S=10 мм/хв |
2,5 |
Різець Р6М5 |
Сталь 45 |
TiN |
V=35 м/хв S=0,1 мм/об |
3,2 |
Фреза торцева Р18 |
40Х |
TiC |
V=20 м/хв S=0,1 мм/зуб |
1,8 |
Свердло Р6М5 |
Сталь 45 |
TiN |
V=15 м/хв S=0,2 мм/хв |
4,5 |
Свердло Р18 |
Сталь 45 |
TiC |
V=20 м/хв S= 0,2 мм/хв |
2,0 |
Довб’як зуборізний Р6М5 |
Сталь 45 |
TiN |
N=30 п.х./хв S=1,2 мм/п.х. |
5,0 |
Економічний аналіз показує, що собівартість зміцнення різального інструменту є не вищою за собівартість інструменту без покриття.
Дані таблиці 1.1 свідчать, що наприклад при зміцненні різця відрізного можна очікувати підвищення стійкості приблизно в 2,5 – 3,5 рази, при чому для раціональності застосування даної технологої зміцнення необхідно, щоб стійкість була підвищена мінімум в 1,4 раза [5]. Тобто застосування методу іонно-плазмового напилення (КІБ) для зміцнення різця відрізного в технології його виробництва дозволить отримати значний економічний ефект.
Таблиця 1.2 – Техніко-економічні показники методів зміцнення різальних інструментів
Метод зміцнення |
Вартість обладнання і впровадження технології, тис. грн. |
Відносна собівартість зміцнення інструменту |
Коефіцієнт підвищення стійкості інструменту |
Без зміцнення |
- |
1,00 |
1,0 |
Хромування |
80 |
0,30 |
1,5 |
Ціанування |
175 |
0,35 |
1,8 |
Азотування |
115 |
0,35 |
2,0 |
Хімічне нікелювання |
82 |
0,50 |
2,5 |
Іонне азотування |
120 |
0,40 |
2,5 |
Іонно-плазмове напилення |
86 |
0,40 |
3,0 |
Детонаційне напилення |
170 |
0,60 |
3,5 |
Дані таблиці 1.2 показують, що іонно-плазмовий метод зміцнення є найбільш оптимальним варіантом при оцінюванні техніко-економічних показників зазначених методів. Компактність обладнання для іонно-плазмового напилення і невисока складність технологічного процесу дає можливість швидко пристосувати його у виробництво. Отже остаточним вибором буде метод іонно-плазмового напилення.
2 Спеціальна частина
2.1 Обґрунтування і вибір методу зміцнення різця відрізного та матеріалів для зміцнення
На основі проаналізованих в попередніх розділах методів зміцнення можна виділити ряд переваг, що обумовили застосувати для зміцнення різця відрізного технологію іонно-плазмового напилення:
- універсальність з точки зору отримання одношарових, багатошарових, комбінаційних покриттів на основі нітридів, карбідів, оксидів, боридів металів;
- відносно невисока собівартість нанесення покриття TiN на різальний інструмент;
- можливість нанесення покриття на будь-який матеріал;
- значне підвищення зносостійкості різального інструменту;
- відносно низький температурний режим процесу – 400 – 550 ºС.
Принцип дії установок для іонного-плазмового напилення оснований на таких фізичнихявищах, як іонізація нейтральних частинок газу, тліючий розряд у вакуумі та розпилення матеріалів бомбардуванням пришвидшеними іонами [6].
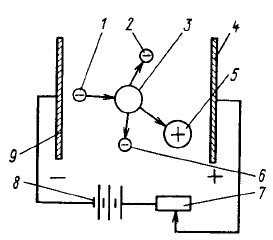
Рисунок 2.1– Процес іонізації [6]:
1,2 – пришвидшений і відбитий електрони; 3 – нейтральна частинка газу; 4 – анод; 5 – іон; 6 – вибитий вторинний електрон; 7 – резистор; 8 – блок живлення; 9 – катод
Суть іонізації частинок газу полягає в наступному. Газ, що знаходиться між двома електродами завжди містить певну кількість вільних електронів. Якщо між електродами створити електричне поле, то це поле буде пришвидшувати електрони (рисунок 2.1). При зустрічі з нейтральною частинкою 3, пришвидшений первинний електрон 1 виштовхує з неї вторинний електрон 6, перетворюючи нейтральну частинку в позитивно заряджений іон 5. таким чином з’являється пара заряджених частинок. Відбитий електрон 2 і вторинний електрон 6 в свою чергу пришвидшуються електричним полем і при взаємодії з нейтральними частинками газу знову утворюють по парі заряджених частинок. Таким чином розвивається лавиноподібний процес утворення в газовому середовищі двох видів заряджених частинок, а в даному випадку газ стає електричним провідником.
1 – катод; 2 – темний катодний простір; 3 - вакуумний балон; 4 – позитивний сяючий стовп дуги; 5 – анод
Тліючий розряд є одним з видів стаціонарного розряду в газах. Його суть показано на рисунку 2.2. З обох сторін у вакуумний скляний балон 3 впаяні два електрода – анод 5 і катод 1. При тиску 0,1-10 Па і подачі напруги 2-4 кВ в результаті іонізації газу в балоні виникає світіння, яке є ознакою тліючого розряду. Утворюються області темного катодного простору 2 та позитивно заряджений світловий стовп 4. При подальшому русі електрона до анода він здатний багатократно іонізовувати частинки газу, таким чином утворюється сяючий стовп дуги. Світіння стовпа дуги пояснюється збудженням нейтральних молекул газу при зіткненні з електронами. Іони, що опиняються на границі катодного простору, пришвидшуються в напрямку катода сильним електричним полем, бомбардують і розпилюють його. Одночасно з розпиленням катода іони вибивають електрони з його поверхні, підтримуюючи розряд [6].
Таким чином тліючий розряд є генератором іонів, необхідних для ефективного бомбардування катода і його розпилення. Іонне розпилення можна пояснити з позиції імпульсного механізму дії прискорених іонів на поверхневі частинки матеріалу. При розпиленні матеріалу, іон 1 передає імпульс енергії його атому, який в свою чергу може передати його іншим атомам, викликавши каскад зіткнень (рисунок 2.3).
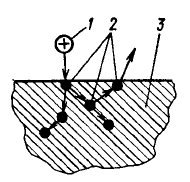
Рисунок 2.3 – Схема іонного розпилення [6]:
1 – іон; 2 - поверхневий атом; 3 – розпилюваний матеріал
Показником ефективності процесу напилення є коефіцієнт розпилення, що виражається числом вибитих частинок розпиленого матеріалу, віднесених на один бомбардуючий іон, і зазвичай складає від кількох долей десятків до кількох одиниць. Він залежить від енергії іона, його маси, кута падіння, розпиленого матеріалу і стану поверхні.
Таблиця 2.2 – Коефіцієнт розпилення S та швидкість росту покриття для деяких матеріалів [7]
Матеріал, що розпилюється |
S, атом/іон |
Швидкість осадження, нм·с-1 |
Матеріал, що розпилюється |
S, атом/іон |
Швидкість осадження, нм·с-1 |
Si |
0,5 |
6,7 |
G |
1,2 |
12,8 |
Ti |
0,6 |
7,8 |
Cr |
1,3 |
16,6 |
Ta |
0,6 |
7,8 |
Pt |
1,6 |
21,0 |
W |
0,6 |
7,8 |
Cu |
2,8 |
30,0 |
Nb |
0,65 |
8,4 |
Pd |
2,4 |
31,2 |
Mo |
0,9 |
11,7 |
Au |
2,8 |
36,7 |
Al |
1,2 |
12,7 |
Ag |
3,4 |
44,2 |
В загальному вигляді процес іонно-плазмовго напилення покриття складається з наступних етапів [7]:
- випаровування напилюваною матеріалу;
- транспортування напилюваного матеріалу па поверхню, яка напилюється;
- стикання напилюваних частинок з поверхнею, яка напилюється;
- утворення центрів конденсації та ріст острівців осадженого матеріалу;
- зливання острівців осадженого матеріалу у суцільну плівку;
- ріст покриття необхідної товщини.
Принципова схема методу.Основними технологічними параметрами процесу КІБ є від’ємний потенціал, що подається на інструментальну основу Uоп, величина сили струму дуги Iді тиск азоту у вакуумній камері Р. Для нанесення нітриду титану на різальний інструмент встановлено межі вибору технологічних параметрів: Uоп= 100...200 В, Iд= 80...140 А, Р= 0,4...0,9 Па, температура основи Тп= 525±10°С. Період іонного очищення – 6-8 хвилин, тривалість осадження τконд= f (h) залежить від необхідної товщини покриття [9].
Схема установки для нанесення зносостійких покриттів ННВ6.6-И1 показана на рисунку 2.4.
Рисунок 2.4 – Схема установки для іонно-плазмового напилення методом КІБ [11]:
1 – пірометр; 2 – вакуумна камера (анод); 3 – блок контролю температури; 4 – високовольтне джерело живлення струму; 5 – блок живлення опорної напруги; 6 – виріб; 7 – подача реакційного газу; 8 – вакуумна система; 9 – вентиль подачі газу; 10 – електродуговий випаровувач з катодом; 11 – автоматичний натікач газу; 12 – вентиль балонний з редуктором і манометрами; 13 – джерело живлення вакуумної дуги
Установка складається з таких основних вузлів: вакуумної камери, системи створення вакууму і подачі реакційного газу, джерел живлення, системи водяного охолодження, блоку управління. Інструмент 6, що підлягає зміцненню розміщується в спеціальному приспосібленні на столі, який з’єднаний з механізмом обертання (рисунок 2.4). Далі з допомогою форвакуумних і дифузійного паромасляного насосів вакуумної системи 8 у вакуумній камері 2 створюють вакуум порядку 0,001...0,006 Па і подається напруга на підложку (1,0 - 1,2 кВ). Одночасно йде процес нагрівання інструменту на підложці до заданої температури (500 – 530 ºС). Таким чином проходить процес іонного бомбардування, що проходить 5 – 10 хвилин. Після закінчення циклу іонного бомбардування в вакуумну камеру подається азот під тиском 0,3 – 1,3 Па, встановлюються необхідні значення напруги підложки і сили струму дуги і протягом заданого інтервалу часу проходить процес осадження TiN на різальний інструмент. Після закінчення процесу осадження покриття інструменти охолоджують в вакуумній камері до 150 ºС.
Розрахунок режимів нанесення TiN покриття.
Для визначення оптимальних значень температури основи при осадженні покриття, забезпечуючих найкращі робочі властивості інструмента, покриття нітрид титану наносилось на ріжучі пластини зі сталі Р6М5. Рівень температури поверхні основи підтримувався при допомозі додаткового джерела нагрівання і становив в кожному експерименті 300, 400, 500 і 600°С. Інші дані: сила струму дуги Iд=120 А, опорна напруга Uоп= 150 В, тиск азоту р= 6,5·10-1 Па, час іонного очищення – 10 хвилин, час осадження – 10, 20, 30, 40, 50 і 60 хвилин [9].
Сила струму дуги має значний вплив на товщину покриття. З підвищенням сили струму товщина покриття росте (рисунок 2.5[лист КП.ТВ-11.00.000 ГР]).
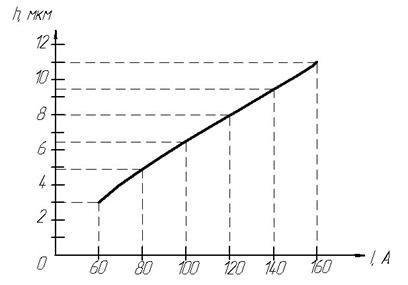
Рисунок 2.5 – Залежність товщини покриття від сили струму дуги випаровувача
Ріст товщини покриття з часом носить прямолінійний характер (рисунок 2.6 [лист КП.ТВ-11.00.000 ГР]). Проте з часом зростає величина макронапружень, тому час осадження повинен бути не більший 60 хвилин.
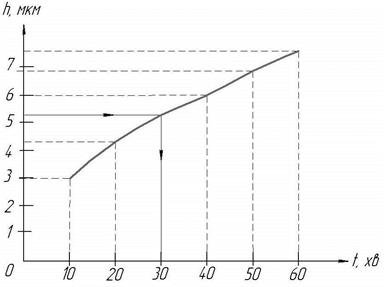
Рисунок 2.6 – Залежність товщини покриття від часу осадження
Для встановлення впливу технологічних параметрів на основні характеристики покриттів вибирались наступні інтервали: Uоп= 0...400 В, Iд= 60...160 А, Р= 0,067...1,33 Па, температура основи Тп= 525±10°С. Період іонного очищення – 6-8 хвилин, процес осадження тривав 30 хвилин. Після проведення процесу осадження покриттів, було виміряно мікротвердість поверхневих шарів, проведено рентгеноструктурний аналіз, а також випробування покриттів на стійкість.
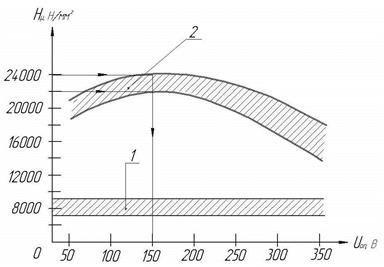
Рисунок 2.7– Залежність опорної напруги від мікротвердості:
1 – покриття TiN; 2 – інструментальної основи
Мікротвердість покриття в 2-3 рази рази перевищує мікротвердість основи і становить приблизно 24000 Н/мм2. в межах зміни напруги від 50 до 300 В, мікротвердість практично не змінюється. Незначне зниження спостерігається при Uоп=0...50 В і Uоп= 300 В (рисунок 2.7 [лист КП.ТВ-11.00.000 ГР]).
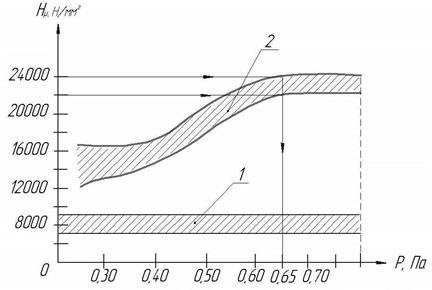
Рисунок 2.8 – Залежність тиску реакційного газу в камері на мікротвердість:
1 – покриття TiN; 2 – підложки
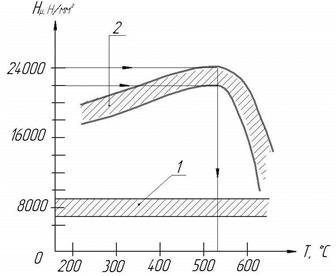
Рисунок 2.9 – Залежність температури підложки від мікротвердості:
1 – зносостійкого покриття TiN; 2 – підложки із швидкоріжучої сталі
Значний вплив на мікротвердість має тиск азоту в камері (рисунок 2.8 [лист КП.ТВ-11.00.000 ГР]). З рисунка видно, що з підвищенням тиску азота в камері від 0,013 до 0,665 Па мікротвердість покриття зростає майже в 2 рази. При подальшому підвищенні тиску азота мікротвердість майже незмінна. Також помічено, що з пониженням опорної напруги від 400 до 0 В колір покриття змінюється від золотистого до світло-жовтого. При всіх досліджених значеннях сили струму покриття має золотисто-жовтий колір. Зі зміною тиску азота в камері колір покриття міняється від світло-золотисто-жовтого (Р=0,065 Па) до темно-золотисто-жовтого (Р=1,33 Па) і до світло-сірого (Р=0,013 Па). Зміни товщини покриття при зміні опорної напруги практично не відбувається.
Випробування на стійкість проводили при точінні сталі ШХ-15 в умовах ефективного використання інструментів з покриттями: v= 0,61 м/с, s= 0,21 мм/об, t= 1мм. Спостерігається значне підвищення стійкості інструменту з підвищенням температури конденсації з 300 до 500°С (рисунок 2.11). При температурі 600°С працездатність інструмента різко знижується через термічне знеміцнення основи. Отже мікротвердість покриття грає велику роль в підвищенні терміну експлуатації різального інструменту (рисунок 2.9).
Мікротвердість покриття мало залежить від величини струму дуги плазмового випаровувача (рисунок 2.10). Незначне зниження спостерігається в покриттях сконденсованих при Iд= 60 А, що викликано їх недостатньою товщиною, а також значне розсіяння значень мікротвердості при Iд= 150 А і вище.
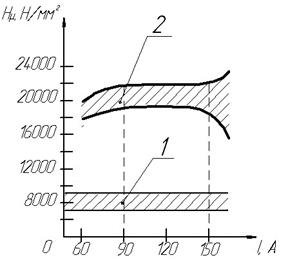
Рисунок 2.10 – Залежність сили струму дуги випаровувача від мікротвердості:
1 – покриття; 2 – підложки
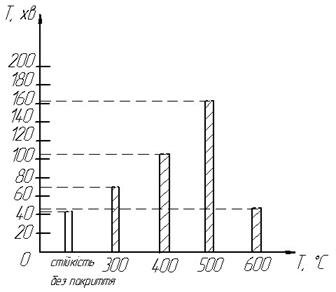
Рисунок 2.11 – Залежність стійкості напиленого швидкорізального інструменту від температури підложки в процесі конденсації покриття [9]
Таким чином для нанесення нітриду титану на різальний інструмент встановлено межі вибору технологічних параметрів: Uоп= 100...200 В, Iд= 90...150 А, Р= 0,4...0,9 Па, температура основи Тп= 525±10°С. На основі математичного моделювання процесу іонно-плазмового напилення і експериментальних даних виведено рівняння, що дозволяють розрахувати приблизну стійкість інструменту К і товщину покриття TiN h [10]:
;
;
де t – час іонного бомбардування підложки (5-10), хв;
Р – тиск азоту в камері, мПа;
U – опорна напруга на підложці, В;
t1 – час осадження покриття, (30)хв;
I – сила струму дуги, А.
Розрахункова стійкість інструменту:
хв.
Розрахункова товщина покриття:
мкм.
Отже основними параметром по вибору режимів осадження покриття буде діапазон мікротвердості (22000-24000 МПа) згідно вимог до різального інструменту. Таким чином вибрано наступні параметри:
- товщину покриття h – 5 мкм;
- час осадження покриття – 30 хвилин;
- сила струму дуги I – 120 А
- опорна напруга на підложці U – 150 В;
- тиск азоту в камері Р – 0,65 Па.
Вибір матеріалів для зміцнення різця відрізного . Для реалізації даної технології зміцнення, а саме отримання зносостійкого покриття TiN, в якості основних матеріалів потрібно мати в необхідній кількості титан технічної чистоти марки ВТ і азот. Для потреб іонно-плазмового напилення розроблені спеціальні циліндрчні титанові катоди-випаровувачі ВТ1-0.
Титан технічної чистоти марки ВТ1-0 поставляється у вигляді циліндричних катодів з найбільшим діаметром 80 мм. Максимально допустимий вміст домішок – 0,3 %. Фізико-механічні властивості титанових катодів ВТ1-0 наведені в таблиці 2.1.
Таблиця 2.1 – Характеристика титану марки ВТ1-0 [12]
Властивість |
Величина (20 ºС) |
Температура плавлення,ºС |
1665 |
Густина, г/см3 |
4,51 |
Теплопровідність, кал/см·с·град |
0,04 |
Коефіцієнт лінійного розширення, *106, град-1 |
8,9 |
Модуль пружності Е, кгс/мм2 |
11200 |
Ударна в’язкість ан, кгс·м/см2 |
12 |
Границя міцності σв, кгс/мм2 |
46 |
Відносне видовження δ, % |
30 |
Твердість по Брінелю, кгс/мм2 |
145 |
Оскільки в якості зносостійкого покриття буде нітрид титану, то в якості реакційного газу буде застосовано азот високої чистоти (99,994%) ГОСТ 9293-74, для виключення протікання небажаних фізико-хімічних процесів у вакуумі. Азот поставляється в якості газу поставляється в балонах місткістю 40 л під тиском 15 і 20 МПа. Граничний об’єм газоподібного азоту рівний 860,4 дм3/кг при тиску 105 Па і температурі 20°С.
Таблиця 2.2 – Характеристика стального балону з азотом, місткістю 40 л [13]
Характеристика |
Величина |
Об’ємний вміст азоту, % |
99,994 |
Об’ємний вміст кисню, % |
0,005 |
Масова концентрація водяних парів, г/м3 |
0,005 |
Робочий тиск, МПа |
15 |
Випробовувальний тиск, МПа |
22,5 |
Кількість газу в балоні, л |
5700 |
Колір балону |
Чорний |
Надпис на балоні |
Азот |
Колір надпису |
Жовтий |
Маса балону,кг |
58,5 |
2.2 Розробка технології зміцнення різця відрізного
Технологічний процес виготовлення і зміцнення відрізного різця може бути поділений на ряд стадій: одержання заготовки, обробка шляхом механічної обробки для надання інструменту заданих геометричних розмірів і форми, термічна обробка, заточування і доводка. Для відрізного різця марки М2130-0003 дана технологія зберігається, але додатково буде проведена фінішна операція по зміцненню поверхні методом іонно-плазмового напилення.
Вихідними заготовками для різців є прутки відповідних розмірів із швидкорізальної сталі. Окремі заготовки одержують шляхом розрізання прутків дисковою пилою на відрізному верстаті. Відрізні різці марки М2130-0003 виготовляються однорідними.
На стадії механічної обробки заготовкам надають відповідних геометричних розмірів і форми. Для цього здійснюють фрезерування і шліфування опорних і робочих поверхонь інструменту. Фрезерування проводять на вертикально-фрезерних верстатах торцевими фрезами. Для підвищення продуктивності обладнання передбачається одночасна обробка десяти різців у спеціальному поворотному приспосібленні (рисунок 2.12)[14].
Рисунок 2.12 – Поворотне приспосіблення для різців [14]:
1 – корпус; 2 – змінний клин; 3 – болти; 4 – планка
Торцеве фрезерування забезпечує шорсткість 5-го класу і високу продуктивність. Шліфування опорних поверхонь здійснюється на плоскошліфувальних верстатах. Таким чином отримуємо поверхні з малою шорсткістю.
Стадія термічної обробки включає в себе термообробку (гартування і відпуск) для підвищення фізико-механічних властивостей, відповідно надання більшої зносостійкості і теплостійкості різальному інструменту. Термічну обробку дрібнорозмірного інструменту можна проводити в камерних печах, в соляних ваннах, на установках СВЧ. В даному випадку гартування і відпуск різців буде проводитись в хлоро-барієвих ваннах, оскільки цей спосіб має ряд суттєвих переваг: рівномірність нагрівання, можливість місцевого нагрівання, захист від окислення при нагріванні. Для одержання високолегованого і стійкого мартенситу швидкорізальну сталь необхідно гартувати при високих температурах. Інструмент із швидкоріжучої сталі підлягає ступеневому нагріванні до 400-500, 780-840 і до 1220-1240°С.
Охолодження сталі при гартуванні до температури мартенситного перетворення повинно бути швидким, щоб аустеніт не встиг перетворитись в проміжні структури. Швидкорізальна сталь одержує добру теплостійкість при пришвидшеному охолодженні в області температур 900-950°С і в області перлітного перетворення 400-500°С, так як повільне охолодження сприяє виділенню карбідів із аустеніту. Структура швидкорізальної сталі після гартування містить мартенсит, залишковий аустеніт і карбіди. Тому, для повного перетворення залишкового аустеніту, відпуску первинного і вторинного мартенситу і зняття залишкових напружень проводять трьохкратний відпуск.
Заточування різців може виконуватись у дві операції. Попереднє і остаточне заточування проводиться по задній і передній поверхнях. Операції здійснюються на універсально-заточувальних верстатах. Попереднє заточування – абразивними кругами ЭБ, кінцеве – алмазними кругами АЧК. Шорсткість шліфованих опорних поверхонь різця не більше Ra=2,50 мкм, заточених поверхонь 0,63 мкм.
Операція іонно-плазмового зміцнення є завершальною, оскільки її результат не має негативного впливу на розміри,форму чи механічні властивості інструменту. Для реалізації процесу буде використано установку для іонно-плазмового напилення типу „Булат” марки ННВ6.6-И1.
Таблиця 2.4 – Технічні характеристики установки ННВ6.6-И1 [10]
Найменування характеристик |
Норма характеристик |
Розміри робочої камери, мм Діаметр Висота |
600+30 600+20 |
Кількість електродів |
3 |
Максимальне навантаження на вал, кг |
92 |
Максимально допустиме навантаження на вісь планетарного механізму, кг |
8 |
Швидкість осадження покриття, мкм/год |
13-40 |
Тривалість циклу зміцнення, год |
Від 2,0 до 2,5 |
Номінальна сила струму блока живлення, А |
20 |
Споживча потужність, кВт |
50+5 |
Залишковий тиск в камері, Па |
Від 6,65·10-3 до 6,65·10-1 |
Розхід води, м3/год |
2 |
Маса установки, т |
3,1 |
Весь технологічний цикл зміцнення відрізних різців з нанесенням покриття TiN полягатиме в наступних операціях:
- підготовка інструменту (час на завантаження 15-20 хвилин);
- забезпечення вакууму в камері (30- 45 хвилин );
- іонне бомбардування і осадження TiN покриття (35-40 хвилин);
- охолодження інструменту (25- 45 хвилин);
- підйом камери, видалення металічної пилу, відвантаження інструментів, установка наступної партії інструментів (7-10 хвилин).
Загалом технологічний процес зміцнення різця відрізного марки М2130-0003 можна представити у вигляді таблиці х.х
Таблиця 2.5 – Технологічний процес зміцнення різця відрізного марки М2130-0003
№ п\п |
Назва операції |
Обладнання, різальний інструмент |
Зміст операції, режими, вимірювальний інструмент |
005 |
Заготівельна |
Верстат відрізний 8А240N = 10 кВт Пила Ø 400 мм ГОСТ 4047-82 |
Розрізати прутки на заготовки в розмір. V= 15 м/хв, S= 2 мм/об. Лінійка масштабна. |
010 |
Фрезерна |
Верстат вертикально-фрезерний 6М12П N = 7 кВт Фреза торцева Ø 63 мм ГОСТ 22085-76 |
Фрезерувати опорні поверхні витримуючи розміри. V= 200 м/хв, S= 500 мм/хв. Штангенциркуль. |
015 |
Фрезерна |
Верстат вертикально-фрезерний 6М12П N = 7 кВт Фреза торцева Ø 63 мм ГОСТ 22085-76 |
Фрезерувати під кутом 15 °С витримуючи розміри.V= 180 м/хв, S= 350 мм/хв. Шаблон. |
020 |
Шліфувальна |
Верстат плоскошліфувальний 3Е710А N = 4 кВт Круг абразивний ПП250*75*50 СМ2-1,6 ГОСТ 2424 – 83 |
Шліфувати заготовки витримуючи розміри. V= 30 м/с, Sо= 32 мм/хід, Sв= 0,015 мм/хід. Зразки шорсткості ГОСТ 9378-75 |
025 |
Термічна |
Електрованна соляна СВС 60/13 N = 60 кВт |
Загартувати. Відпустити. Гартування в розчині солі BaCl при температурі 1220-1230°С. Відпуск при температурі 540-580°С. |
030 |
Заточувальна |
Верстат універсально-заточувальний 3Б641 N = 0,7 кВт Круг абразивний ЧК 250*75*50 ЭБ16-25С2К ГОСТ 2424 – 83 |
Заточити попередньо передню і задню поверхні під кутами 5°±30′ і 10°. V= 30 м/с, Sпоп= 0,5 мм/п.хід, Sпов= 2,0 мм/п.хід. Шаблон. |
035 |
Заточувальна |
Верстат універсально-заточувальний 3Б641 N = 0,7 кВт Круг алмазний АЧК 125*5*3 ГОСТ 24747-81 |
Заточити кінцево передню і задню поверхні під кутами 5°±30′ і 10°. V= 40 м/с, Sпоп= 0,03 мм/п.хід, Sпов= 1,5 мм/п.хід. Шаблон. |
040 |
Клеймильна |
Верстат клеймильний МФ-16 Клейма машинні твердосплавні ВК20 |
Маркувати М2130-0003. V= 28 хід/хв. |
045 |
Напилення |
ННВ 6.6-И1 N = 30 кВт Мікротвердомір. |
Нанесення зносостійкого покриття ТіN. I=120 A, U= 150 В, P= 0,7 Па. |
050 |
Контрольна |
Стіл для вихідного контролю. Мікротвердомір ПМТ-3. |
Штангенциркуль, шаблон, |
2.3 Проект дільниці розміщення обладнання для зміцнення різця відрізного
Вибір розмірів дільниці, постів, пристроїв, приспосібленьу даному розділі вибираємо розміри цеху та кількість прольотів в залежності від необхідної площі на одиницю обладнання [15]. Планування верстатного відділення дільниці проводиться по типам верстатів з додержанням загальної послідовності операцій виготовлення і зміцнення типових деталей. При цьому зосередимо в одному прольоті обладнання більш менш близьких розмірів, таким чином верстати будуть розміщуватися в одному прольоті, а обладнання для термообробки, іонно-плазмового зміцнення, контрольний пункт і складські приміщення в другому [лист КП.ТВ-11.00.000 Д].
При розміщенні обладнання передбачено найкоротші шляхи руху кожної деталі в процесі, для того, щоб спростити транспортування деталей, які виготовляються.
При розробці загальної компоновки дільниці розміщуємо його відділення у відповідності з послідовністю операцій, це можна досягнути при розміщенні відділень дільниці по слідкуючій схемі:
- склад матеріалів;
- верстатне відділення;
- термічне відділення;
- відділення нанесення іонно-плазмових покриттів;
- місце контролера, місце майстра і контрольний стіл;
- склад готової продукції.
Кожному типу обладнання дається умовне графічне зображення.
Віддаль між боковою стороною верстату від стіни (або виступаючої колони) – 500 мм.
Віддаль між фронтом верстату і стіною (колоною) – 800 мм.
Віддаль між верстатами – 900 мм.
Ширина проїзду – 3000 мм.
Необхідна площа термічного відділення, на одну електрованну – 30 м2.
Необхідна площа відділення для нанесення іонно-плазмових покриттів, на одну установку типу „Булат” – 16 м2.
Необхідна площа контрольного відділення, місце майстра – 12 м2.
Складські приміщення – 40 м2.
Загальна площа дільниці – 216 м2.
Робочі місця верстатників сплановані так, щоб забезпечити безпеку тих, що працюють, а також швидкій евакуації їх в екстремальних випадках і забезпечення ремонтних робіт.
До устаткування на ділянці підводиться СОЖ, стиснене повітря, газ, вода, електроенергія.
Для пожежної безпеки передбачені:
- пожежний кран;
- пожежний щит;
- ящик з піском.
2.4 Охорона праці і техніка безпеки при зміцненні різального інструменту
В даному розділі увага буде звернута в основному на охорону праці при інструментальному виробництві.
Основними умовами безпечної роботи при виконанні операцій по механічній обробці є правильна організація робочого місця, користування лише справними інструментами, суворе дотримання виробничої дисципліни та вимог безпеки.
Усі частини верстатів і механізмів, що обертаються, а також оброблювані заготовки з частинами, що виступають, повинні мати захисні огородження.
Небезпеку становлять внутрішньозаводський автомобільний і безрейковий електротранспорт, ручні вагонетки, візки, а також рух робітників у вузьких проходах чи на шляхах, де працює вантажопідйомний транспорт.
Для транспорту, що рухається, встановлюють різні сигнали — звукові (дзвінки, сирени) і світлові (лампи різних кольорів — червоного, жовтого, зеленого), які треба знати і дотримувати.
При безпосередньому дотику до струмоведучих частин (вимикачів, рубильників тощо) чи до металевих предметів, які випадково виявилися під напругою, виникає небезпека ураження електричним струмом. У місцях, де є електричні установки, вивішують попереджувальні написи (наприклад, «Небезпечно!», «Під струмом!») або ставлять умовні знаки.
Електроінструменти слід підключати до електричної мережі з допомогою шлангового кабеля, який має спеціальну жилу, що служить для заземлення і занулення, через штепсельну розетку, одне гніздо якої з'єднано з землею чи з нульовим проводом. На штепсельній вилці контакт для з'єднання корпуса з землею роблять більшої довжини, ніж інші струмоведучі контакти. Завдяки такій будові при вмиканні електроінструмента спочатку відбувається заземлення чи занулення, а потім вмикаються струмоведучі контакти.
Балони з газами зберігають і транспортують тільки з нагвинченими на їх горловини запобіжними ковпаками і заглушками на бокових штуцерах вентилів. При транспортуванні балонів не допускаються поштовхи і удари. До місця робіт балони доставляють на спеціальних візках чи носилках. Забороняється зберігати балони з киснем в одному приміщенні з балонами пального газу, з барабанами карбіду кальцію, лаками, мастилами і фарбами. В цілях безпеки кисневі балони фарбують в синій колір, ацетиленові – в білий, пропан-бутанові – в червоний, азотні – в чорний [16].
При роботі з електроінструментами слід застосовувати індивідуальні засоби захисту — гумові рукавички, калоші та килимки, ізолюючі підставки тощо.
До початку роботи треба:
- надягнувши спецодяг, перевірити, щоб у нього не було звисаючих кінців, рукава застебнути чи закатати вище ліктя;
- перевірити верстат на якому буде здіснюватись робота;
- підготувати робоче місце; звільнити потрібну для роботи площу, видаливши всі сторонні предмети; забезпечити достатню освітленість; заготовити і розкласти у відповідному порядку потрібні для роботи інструменти пристрої, матеріали тощо;
- перевірити справність інструментів, правильність їх заточки і доводки;
- перевірити справність робочого обладнання та його огородження.
Під час роботи:
- міцно затискати в закріплюючих пристроях деталь чи заготовку, а під час встановлення чи зняття її дотримуватися обережності, бо при падінні деталь може нанести травму;
- стружку з верстату чи оброблюваної деталі видаляти лише щіткою;
- не користуватися випадковими підставками чи несправними пристроями;
- не допускати забруднення одягу гасом, бензином, мастилом.
Після закінчення роботи:
- ретельно прибрати робоче місце;
- покласти інструмент, пристрої та матеріали на відповідні місця;
- для попередження самозаймання промащеного ганчір'я та виникнення пожежі прибрати його в спеціальний металевий ящик з кришкою, що щільно зачиняється. Найпростіші протипожежні засоби та інвентар — ящики з піском та лопатами, мішечки з піском, пожежний кран, насоси, вогнегасники — мусять бути завжди в наявності та справності. Палаючі матеріали і невелику кількість палаючої рідини гасять піском; гас, бензин, лаки, спирти, ацетон — піною; мастильні масла, оліфу, скипидар —розпиленою водою чи піною.
Вимоги до приміщень і правила утримання вакуумних установок.
1. Приміщення, де змонтовані вакуумні електричні печі, повинні бути сухими, з чистим повітрям ( наявність витяжної вентиляції ).
2. Стіни і стелі приміщень мають бути пофарбовані масляною фарбою, підлогу застелити плиткою, лінолеумом, пластиком та іншими матеріалами, що не утворюють пилюки.
3. Стіни і стелі приміщень, де працюють вакуумні електропечі під тиском більшим 10-2 Па, рекомендується пофарбувати масляною фарбою, а панелі стін викласти кафельною плиткою.
4. В приміщенні не проводити технологічні процеси пов’язані з виділенням парів основ чи кислот.
5. Викид газів із вихлопних отворів вакуумних насосів повинен здійснюватись по трубопроводам за межі приміщення.
6. Приміщення повинно регулярно прибиратись. Прибирання і миття підлоги рекомендується проводити в той час, коли електропіч працює в режимі вакууму.
Вимоги до персоналу, що обслуговує вакуумні електропечі з граничним вакуумом до 10-3 Па.
- До обслуговування вакуумних електропечей допускається персонал, що ознайомлений з інструкціями по обслуговуванню вакуумних електропечей, вакуумного обладнання.
- Персонал повинен мати чистий спецодяг ( халат, головний убір і т.д.)
- Перед входом в приміщення, обладнані вакуумними електропечами одягти спецвзуття, при цьому покидати межі приміщення заборонено.
- Обслуговуючий персонал при роботі з вакуумними електропечами повинен виконувати наступні вимоги:
а - перед початком робіт вимити руки;
б - проводити роботу чистим знежиреним інструментом;
в - не вносити в електропіч бруд, пилюку, воду і т.д.;
г - протирання поверхонь проводити матеріалом, що не залишає ворсу, ниток та інших частинок.
Висновки
Отже розроблена технологія зміцнення різального інструменту (різець М2130-0003) передбачає підвищення зносотійкості в 3,9 раз, що відповідає періоду стійкості інструменту Т=195 хв. Дана технологія може бути впроваджена не тільки в дрібносерійне виробництво, але й у крупносерійне і масове виробництво, завдяки можливості автоматизації процесу. Оскільки собівартість зміцнення відрізного різця рівна не більша половини вартості нового інструменту, то при зміцненні партії різців за один виробничий цикл (500 шт.) з відповідною річною програмою на рівні дрібносерійного чи серійного типу виробництва дозволить отримати значний техніко-економічний ефект.
Список використаних джерел
1. Грановский Г.И. Резание металлов. – М.: Высшая школа, 1985. – 304 с.
2. Фещенко В.Н.Токарная обработка. – М.: Высшая школа, 2005. – 303 с.
3. Мацевитый В.М. Покрытия для режущих инструментов. – Харьков: Вища школа, 1987 – 128 с.
4. Усачев П.П. Повышение износостойкости и прочности режущих инструментов. – К.: Техника, 1981. – 158 с.
5. Шишков В.Д Современные методы упрочнения режущего инструмента. – Л.: ЛДНТП, 1981. – 20 с.
6. Минайчев В.Е. Нанесение пленок в вакууме. – М.: Высшая школа, 1989. – 110 с.
7. Митин Б.С. Порошковая металлургия и напыленные покрытия: Учеб. для втузов. – М.: Металлургия, 1987. – 792 с.
8. Никитин М.М. Технология и оборудование вакуумного напыления - М.: Металлургия, 1992. – 110 с.
9. Внуков Ю.Н. Нанесение износостойких покрытий на быстрорежущий инструмент. – Киев: Тэхника, 1992. – 143 с.
10. Прогрессивная технология нанесения износостойких покрытий на инструмент и его эксплуатация: Обзор. инф./ А.В. Коровкин, Г.А. Усачев, С.С. Кравченко. Тольятти: НИИН-автопром, 1985. – 76 с.
11. Тополянский П.А. Ионно-плазменное напыление износостойких покрытий на инструмент.// Технологии ремонта, восстановления и упрочнения деталей машин, механизмов, оборудования, инструмента и технологической оснастки. Материалы 6-й Международной практической конференции-выставки 13-16 апреля 2004 г. – Санкт-Петербург: СПбГПУ, 2005, с. 323 – 338.
12. Глазунов С.Г., Моисеев В.Н. Конструкционные титановые сплавы – М: Металлургия, 1974, 367 с.
13. Геворкян В.Г. Основы сварочного дела. Учеб. для строит.спец.тех. – М.: Высшая школа, 1985. – 168 с.
14. Космачев И.Г. Карманный справочник технолога-инструментальщика. – Л.: Машиностроение, 1970. – 265 с.
15. Канарчук В.Е. Основы проектирования и реконструкции механических цехов и участков машиностроительных и ремонтных производств. – К.: Вища школа, 1988. – 221 с.
16. Молодык Н.В., Зенкин В.С. Восстановление деталей машин: Справочник. – М.: Машиностроение, 1989. – 480 с.
17. СТП 02070855 – 03-99.
Похожие материалы
... інструментом для створення нових, оригінальних технологічних процесів шляхом комбінування і переміщення методів і умов виконання відомих способів [4Евдокимов, с.7-9]. Розділ 2. Технології поверхневого зміцнення сталевих виробів 2.1 Зміцнення поверхні методом пластичної деформації Ефективними способами зміцнення поверхневого шару є дробоструйна обробка, що дозволяє опрацьовувати сталеві ...
0 комментариев